Header
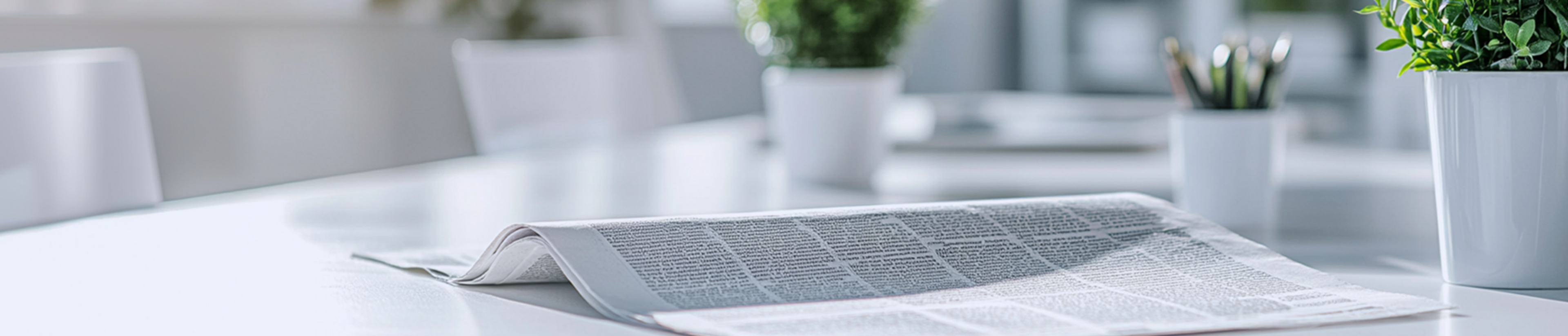
NEWS
More Option
Shaft Components: The Best Choice for CNC Machining
BY: Ningbo Shelley
3 months ago
Shaft Components: The Best Choice for CNC Machining
Introduction
Shaft components are the workhorses of the engineering world, silently transmitting power and motion in countless applications. From simple axles to intricate driveshafts, these versatile parts come in various forms and materials, making them essential building blocks for machinery. CNC machining, with its precision and flexibility, stands out as a preferred method for crafting high-quality shaft components. In this article, we’ll explore why shaft components are critical, the advantages of CNC machining for their production, and key considerations for optimizing their design and manufacturing.
What Are Shaft Components?
Shaft components are mechanical elements designed to transfer torque, support rotating parts, or guide motion within a system. They come in many shapes and sizes, tailored to specific functions:
- Axles: Non-rotating shafts that support wheels or other components.
- Driveshafts: Transmit rotational power between components, common in vehicles and industrial machinery.
- Spindles: Precision shafts used in high-speed applications like CNC machines or turbines.
- Crankshafts: Convert linear motion into rotational motion, vital in engines.
Shafts are typically made from materials like carbon steel, stainless steel, aluminum, or specialized alloys, chosen based on strength, weight, and environmental factors. Their design often includes features like keyways, splines, or stepped diameters to accommodate bearings, gears, or couplings.
Why CNC Machining for Shaft Components?
CNC (Computer Numerical Control) machining is a manufacturing process that uses computer-controlled tools to shape materials with unparalleled accuracy. For shaft components, CNC machining offers several compelling advantages:
1. Precision and Accuracy
Shafts often require tight tolerances—sometimes within microns—to ensure smooth operation and minimal wear. CNC machines excel at producing complex geometries, such as concentric diameters, threaded sections, or intricate splines, with consistent precision. This reduces the risk of misalignment or failure in high-performance applications.
2. Material Versatility
CNC machining can handle a wide range of materials, from soft aluminum to tough titanium alloys. This flexibility allows manufacturers to select the optimal material for a shaft’s specific load, corrosion resistance, or weight requirements without compromising on quality.
3. Customization and Complexity
Unlike traditional manufacturing methods, CNC machining easily accommodates custom designs. Whether it’s a one-off prototype or a production run of unique shafts with non-standard features, CNC machines can adapt quickly, minimizing setup time and costs.
4. Efficiency and Scalability
For small batches, CNC machining offers rapid turnaround without the need for expensive molds or dies. For larger production runs, automated CNC processes ensure repeatability, reducing labor costs and errors. Modern multi-axis CNC machines can even perform multiple operations (turning, milling, drilling) in a single setup, streamlining production.
5. Surface Finish Quality
Shafts often require smooth surfaces to reduce friction and wear, especially in high-speed or heavy-load applications. CNC machining delivers excellent surface finishes, often eliminating the need for secondary polishing or grinding.
Applications of CNC-Machined Shaft Components
Shaft components produced via CNC machining are integral to industries worldwide:
- Automotive: Driveshafts and crankshafts power vehicles with efficiency and reliability.
- Aerospace: Lightweight, high-strength shafts ensure precision in turbines and control systems.
- Industrial Machinery: Spindles and rollers drive manufacturing equipment with minimal downtime.
- Medical Devices: Miniature shafts enable precise motion in surgical tools and diagnostic machines.
- Renewable Energy: Shafts in wind turbines and hydroelectric systems withstand extreme conditions.
Key Considerations for CNC-Machined Shafts
To maximize the benefits of CNC machining for shaft components, consider the following during design and production:
1. Material Selection
Choose materials based on the shaft’s operating environment. For example:
- Steel for high strength and durability.
- Aluminum for lightweight applications.
- Stainless steel or titanium for corrosion resistance in harsh conditions.
Work with your CNC machining partner to ensure material availability and compatibility with their equipment.
2. Design Optimization
- Minimize Stress Concentrations: Avoid sharp corners or abrupt diameter changes, which can lead to fatigue failure.
- Incorporate Tolerances: Specify tolerances that balance performance with manufacturability to avoid unnecessary costs.
- Simplify Features: Where possible, reduce the number of complex features to lower machining time without sacrificing function.
3. Machining Parameters
Collaborate with your CNC machinist to optimize cutting speeds, feeds, and tool paths. Proper parameters reduce tool wear, improve surface quality, and shorten lead times.
4. Quality Control
Implement rigorous inspection processes, such as coordinate measuring machine (CMM) checks or laser scanning, to verify dimensions and tolerances. For critical applications, consider non-destructive testing to detect internal flaws.
5. Cost Management
While CNC machining is cost-effective for precision parts, costs can escalate with overly tight tolerances or exotic materials. Balance performance requirements with budget constraints, and explore batch production to leverage economies of scale.
Future Trends in Shaft Component Manufacturing
As technology evolves, CNC machining for shaft components is becoming even more powerful:
- Automation: Advanced CNC systems with AI-driven toolpath optimization are reducing setup times and improving efficiency.
- Additive Integration: Hybrid machines combining CNC machining with 3D printing allow for complex shaft designs with internal features.
- Sustainability: Manufacturers are adopting eco-friendly materials and energy-efficient CNC processes to meet environmental regulations.
Conclusion
Shaft components are indispensable in engineering, enabling motion and power transfer across industries. CNC machining’s precision, versatility, and efficiency make it the ideal choice for producing these critical parts, from simple axles to intricate spindles. By optimizing material selection, design, and machining processes, manufacturers can deliver high-quality shafts that meet the demands of modern applications.
Whether you’re designing a prototype or scaling up production, partnering with an experienced CNC machining provider is key to success. Ready to start your next shaft component project? Reach out to a trusted machining expert today to bring your vision to life.
Share On
Search
Browse By Categories
Recent Posts
Prestressed Anchorage: Transforming Construction Stability
BY:Ningbo Shelley
Enhancing Structures with Prestressed Anchorage Technology
BY:Ningbo Shelley
Prestressed Anchorage: Enhancing Modern Construction
BY:Ningbo Shelley
Understanding Prestressed Anchorage in Modern Construction
BY:Ningbo Shelley
Prestressed Anchorage: Enhancing Structural Integrity
BY:Ningbo Shelley
Harnessing Prestressed Anchorage in Modern Engineering
BY:Ningbo Shelley
Get In Touch With Us
If you encounter any problems, please contact us in time.We will give you a satisfactory answer as soon as possible.
Contact You
To ensure we can follow up on your inquiry effectively, could you please provide your email address?